Sustainability projects at Ardagh Glass Packaging-Europe
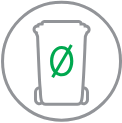
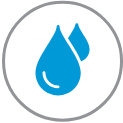
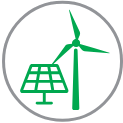
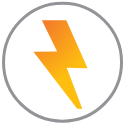
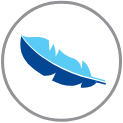

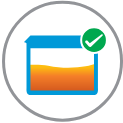
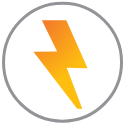
Project type:
Energy
Project name:
Electricity storage AGP-Irvine
Project location:
Irvine, UK
Project aim:
Provide AGP-Irvine with reliable year-round energy for continuous glass production using sustainable battery storage, increasing resilience and energy security.
Key benefits:
This Tesla battery system ensures reliable back-up during peak energy use and returns energy to the grid during low demand.
Description:
Ardagh Glass Packaging implemented Europe's largest behind-the-meter storage system, a Tesla Battery Storage System. This innovative solution not only provides a reliable backup during peak energy consumption but also feeds energy back to the grid during low demand.
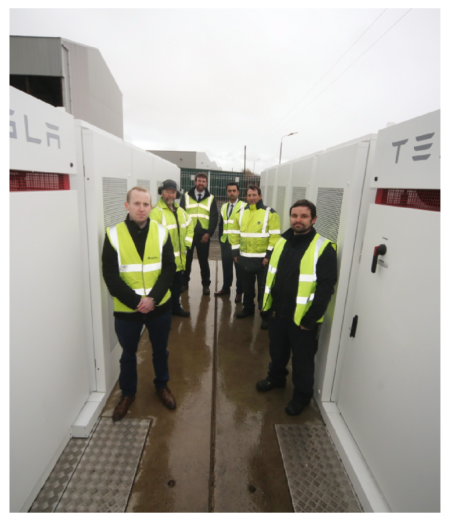
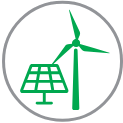
Project type:
Renewable Electricity
Project name:
Onsite solar energy at AGP-Irvine
Project location:
Irvine, UK
Project aim:
An onsite solar installation producing renewable electricity for the AGP-Irvine facility.
Key benefits:
This onsite solar installation is expected to remove the equivalent of c. 356 tonnes of CO₂ annually.
Description:
An onsite, rooftop 1.75 Megawatt Peak solar PV installation of 3842 panels at AGP-Irvine in Scotland is generating onsite renewable electricity, which will add enough electricity back to the grid to remove the equivalent of an estimated 356 tonnes of CO₂ annually.
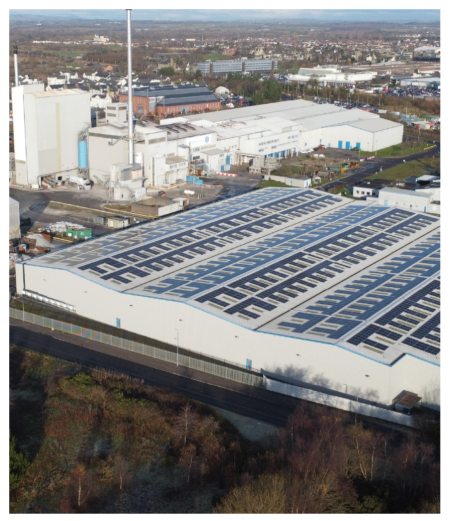
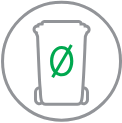
Project type:
Waste
Project name:
Zero Waste to Landfill
Project location:
Irvine UK
Project aim:
To recycle ≥95% of operational waste from each AGP facility.
Key benefits:
Eliminating operational waste from the glassmaking process will reduce AGP’s ecological impact.
Description:
Ardagh Glass Packaging’s Zero Waste to Landfill status recognises the diversion of operational waste from its facilities away from landfills, and the environment. Thirteen AGP-Europe facilities have already reached this status, with the goal for all facilities across AGP-Europe to achieve this by 2030.
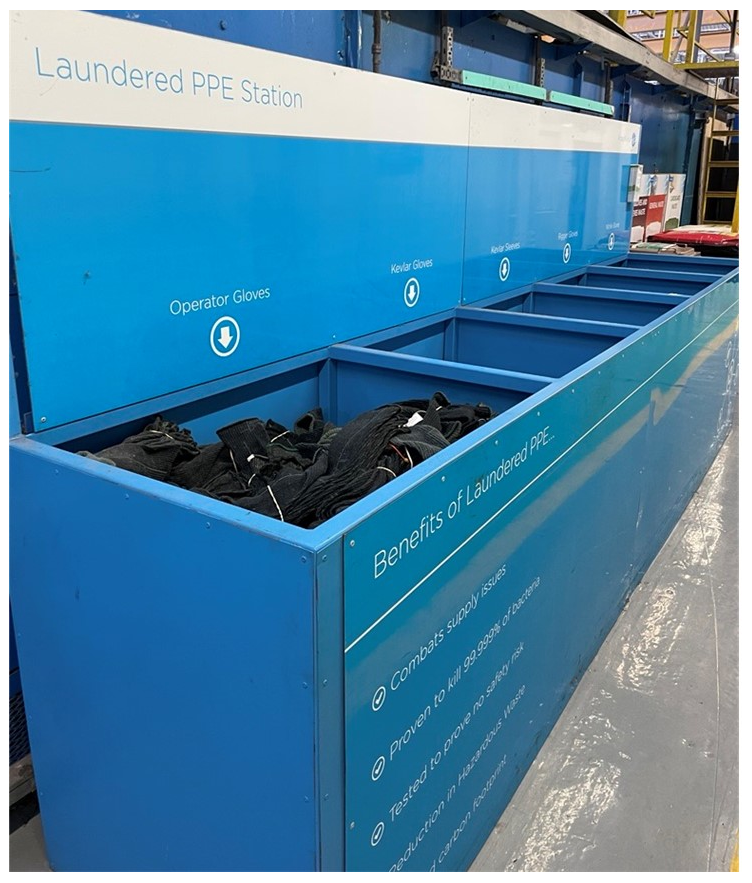
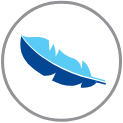
Project type:
Lightweighting
Project name:
Virtual Twin Lightweighting
Project location:
Irvine, UK
Project aim:
To develop a coating that will enable glass containers to be lighter without compromising strength.
Key benefits:
The Virtual Twin project is developing a coating that enables glass containers to be lighter, without compromising strength.
Description:
This R&D lightweighting project between Ardagh Group, Exxergy, Dassault Systèmes and Diageo, aims to develop a coating that will enable glass containers to be lighter without compromising strength. The external coating will reduce naturally-occurring micro-cracks in the glass surface, allowing the glass to be much lighter while maintaining its strength.
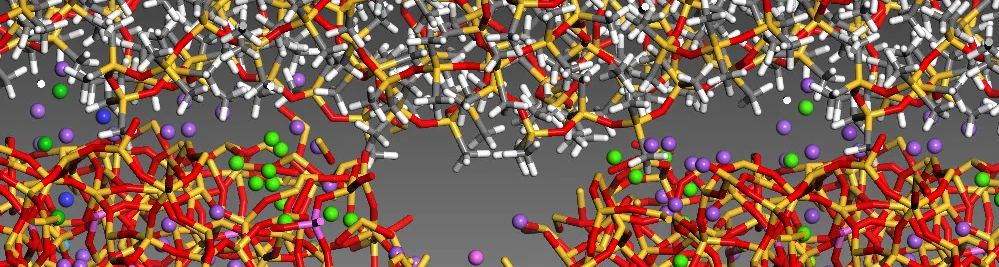
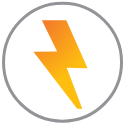
Project type:
Energy
Project name:
Biofuel Trial – Knottingley UK
Project location:
Knottingley, UK
Project aim:
To explore the viability of using biofuel in place of natural gas in the furnace.
Key benefits:
Using biofuel in place of natural gas significantly reduces carbon emissions.
Description:
Ardagh Glass Packaging has successfully completed a trial to produce glass packaging using biofuel in the furnace at its Knottingley, UK facility. This was part of a Glass Futures initiative to explore alternative, sustainable fuels. The trial replaced 100% of the natural gas with lower-carbon biofuel in the furnace, demonstrating that lower-carbon glass packaging can be produced at commercial scale with no compromise on glass quality or process efficiency.
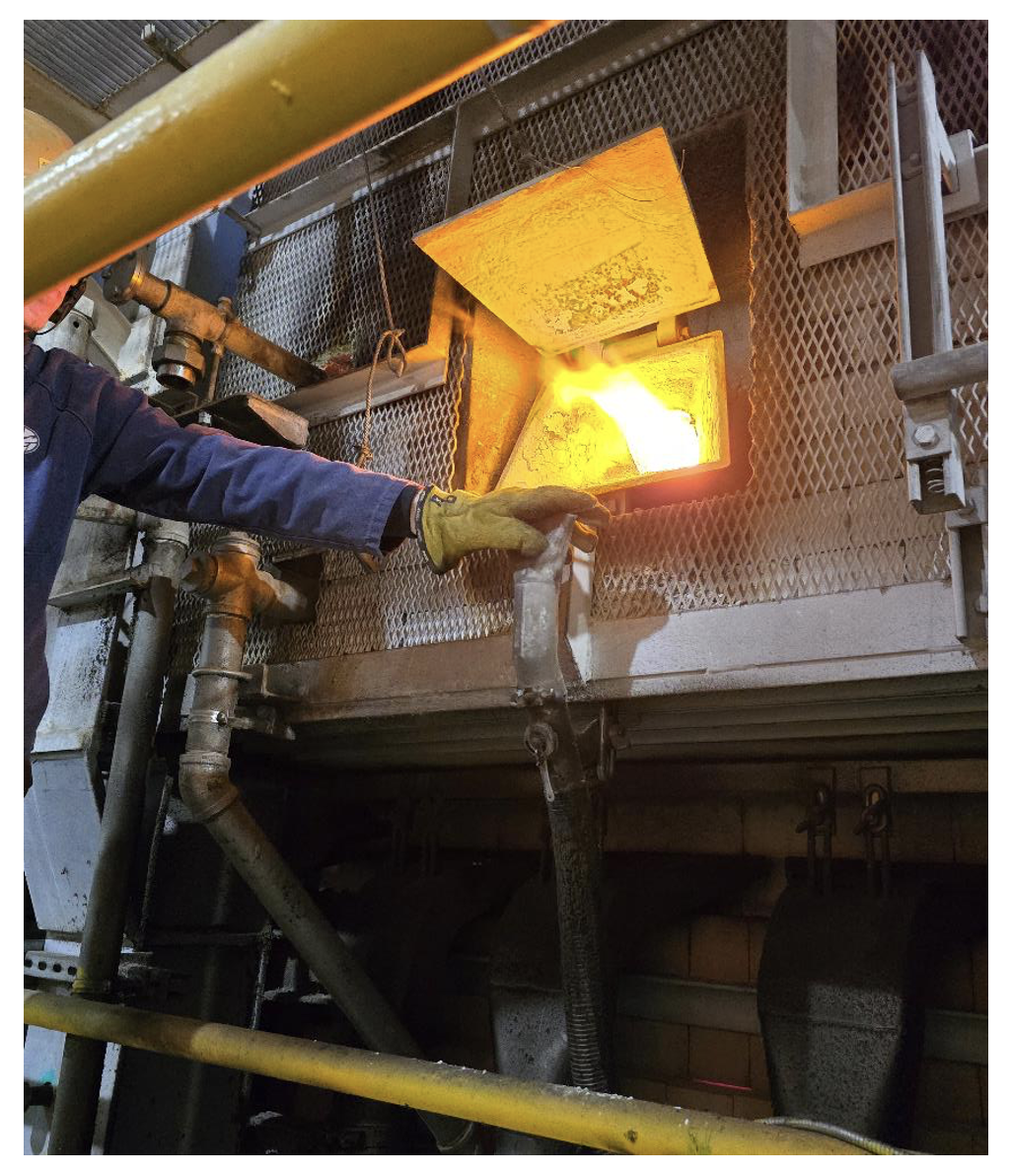
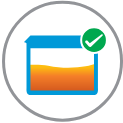
Project type:
Low-carbon melting
Project name:
Efficient Furnace AGP-Doncaster
Project location:
Doncaster, UK
Project aim:
To build a highly sustainable 'Efficient Furnace' that will minimise greenhouse gas emissions from the glass production process.
Key benefits:
This efficient furnace significantly reduces gas consumption, reducing carbon emissions by 14% compared to the previous furnace.
Description:
This state-of-the-art furnace at AGP-Doncaster, UK, uses the latest conventional furnace technology with a more efficient melter, significantly lowering gas consumption and carbon emissions. It includes a gas filtration process with advanced filters to reduce other emissions well below industrial standards, reducing CO₂ by 14% compared to the old furnace.
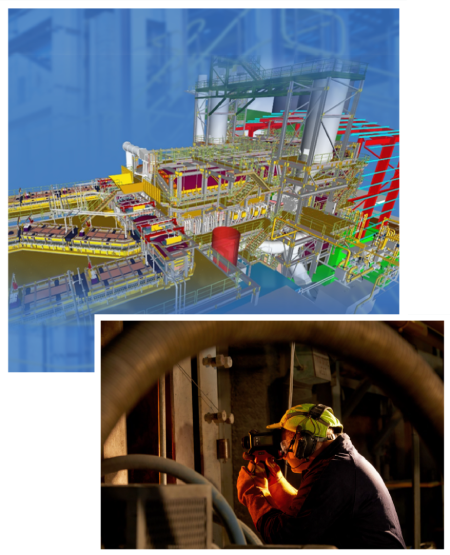
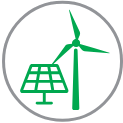
Project type:
Renewable Electricity
Project name:
Renewable electricity at AGP-Moerdijk
Project location:
Moerdijk, The Netherlands
Project aim:
A solar installation producing renewable electricity for the AGP-Moerdijk facility.
Key benefits:
This solar installation is expected to reduce the carbon footprint at AGP-Moerdijk by c. 725 tonnes of CO2 annually.
Description:
AGP's solar installation in Moerdijk, the Netherlands, is expected to generate over 2,500 MWh of electricity per annum, reducing the facility’s carbon footprint by an estimated 725 tonnes of CO₂ annually.
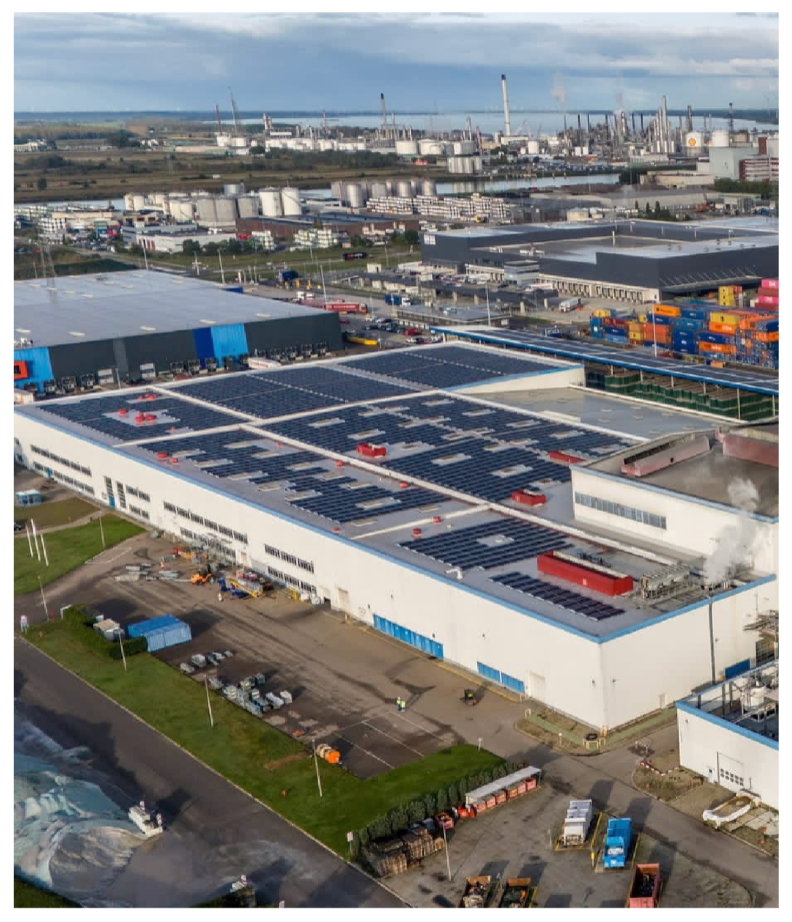
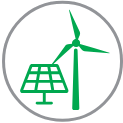
Project type:
Renewable Electricity
Project name:
Renewable electricity at AGP-Dongen
Project location:
Dongen, The Netherlands
Project aim:
A solar installation producing renewable electricity for the AGP-Dongen facility.
Key benefits:
This solar installation is expected to generate over 8000MWh of renewable electricity annually at AGP-Dongen.
Description:
The solar installation at Ardagh Glass Packaging in Dongen, the Netherlands is expected to generate over 8000 MWh of electricity per annum - a significant step in achieving AGP's target to use 100% renewable electricity by 2030.
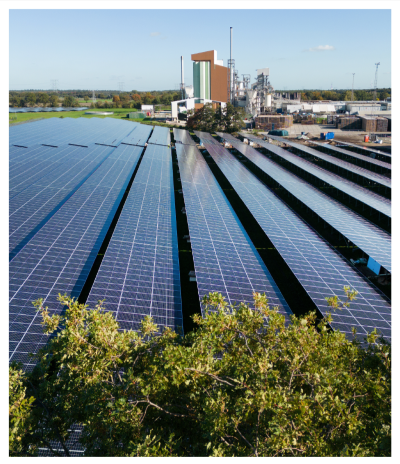
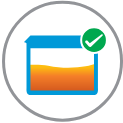
Project type:
Low-carbon melting
Project name:
Next Gen Furnace
Project location:
Obernkirchen, Germany
Project aim:
To reduce CO₂ emissions by operating with up to 80% renewable electricity at the AGP-Obernkirchen facility in Germany.
Key benefits:
The Next Gen Furnace has reduced carbon emissions by 64% per bottle to June 2024.
Description:
AGP's breakthrough Next Gen Furnace has reached a consistent 64% CO2 emissions reduction in 2024, and AGP is striving for more. The CO₂ reduction has been achieved by reaching an average rate of 60% electrical heating in the furnace, and has saved approximately 18,000 tonnes of CO₂ from January to June 2024.
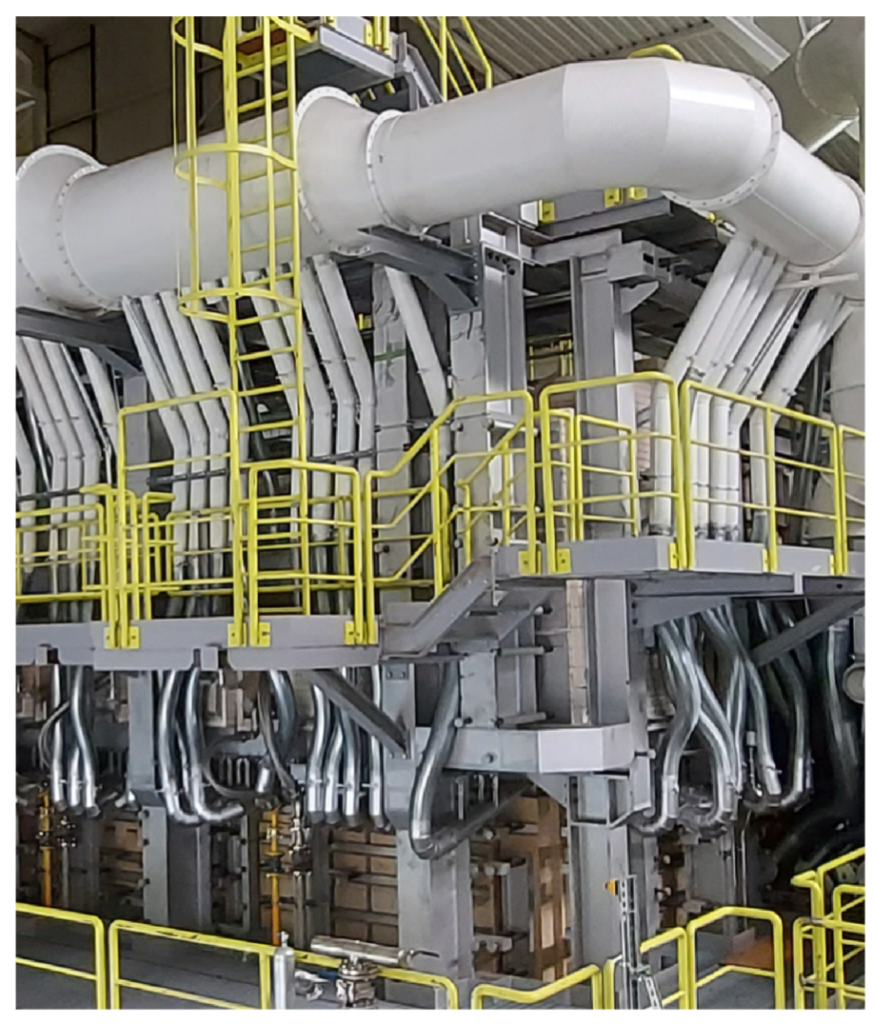
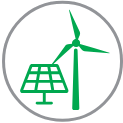
Project type:
Renewable Electricity
Project name:
NextGen Furnace – Solar energy PPA
Project location:
Obernkirchen, Germany
Project aim:
To secure a long-term supply of 100% renewable electricity for AGP’s NextGen Furnace.
Key benefits:
This Power Purchase Agreement will secure an annual solar-powered, renewable electricity supply of c. 100 GWh to AGP’s NextGen Furnace.
Description:
AGP-Europe has entered a PPA with Sunnic Lighthouse to secure a longer-term solar electricity supply to AGP’s NextGen Furnace in Obernkirchen, Germany, with an annual volume of approximately 100 GWh.
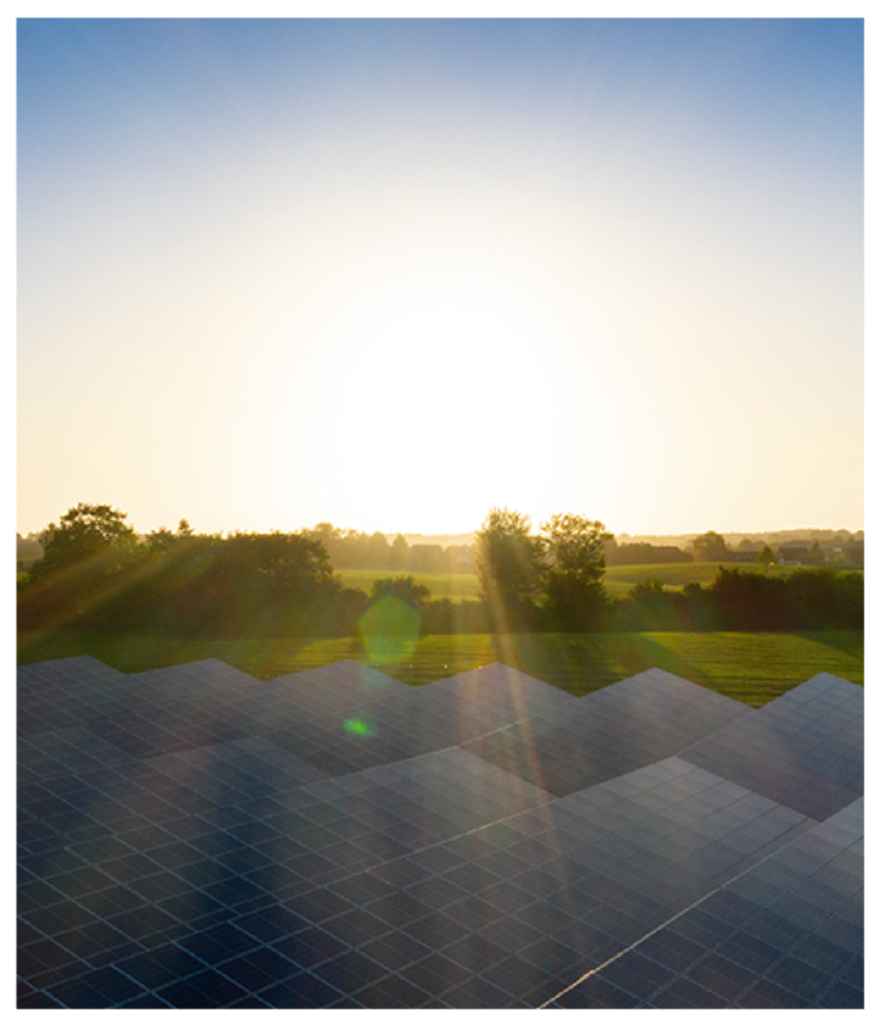

Project type:
Social
Project name:
Ardagh for Education (Germany, also active in North America, Brazil, and Africa)
Project location:
Germany
Project aim:
Ardagh for Education's mission is to give back to our communities through quality STEM education, empowering future generations with 21st-century skills by upskilling educators.
Key benefits:
Ardagh for Education trains teachers and provides students with high-quality STEM learning experiences to equip them with in-demand, 21st century skills.
Description:
Ardagh for Education, a STEM program, enhances teachers' skills through quality training and provides students with hands-on learning to develop 21st-century skills like problem-solving, collaboration, critical thinking and more. To date in 2024, the program has engaged 129 schools in Germany, upskilled 301 teachers and 23 ambassadors, and reached over 6,000 students.
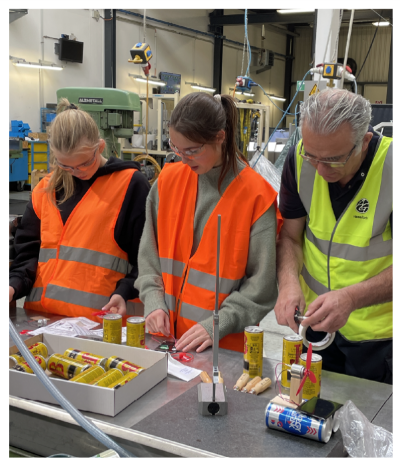
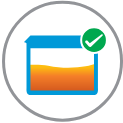
Project type:
Low-carbon melting
Project name:
Efficient Furnace AGP-Germersheim
Project location:
Germersheim
Project aim:
To build a highly efficient regenerative furnace, to minimise carbon emissions from the glass production process.
Key benefits:
AGP-Germersheim's efficient regenerative furnace aims to reduce carbon emissions by c. 23%.
Description:
A conversion from recuperative to regenerative furnace technology, reducing carbon emissions by 23%.
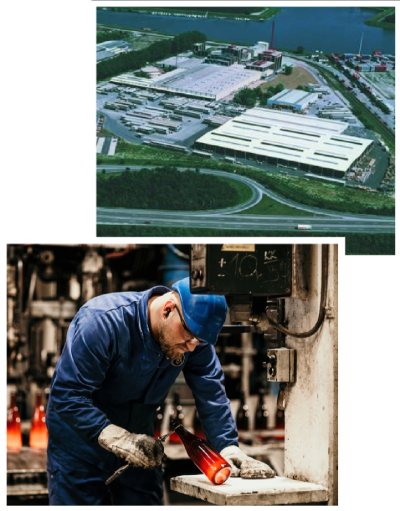
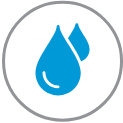
Project type:
Water
Project name:
Water Reduction Project
Project location:
Ujscie, Poland
Project aim:
To deliver a reduction in water usage.
Key benefits:
Closed loop systems replace the use of local groundwater to cool the IS machines, with a 25% reduction in water usage.
Description:
Independent closed loop systems have been installed for clean and dirty water, in place of using local groundwater, to cool the IS machines, delivering a 25% reduction in water usage compared with 2021.
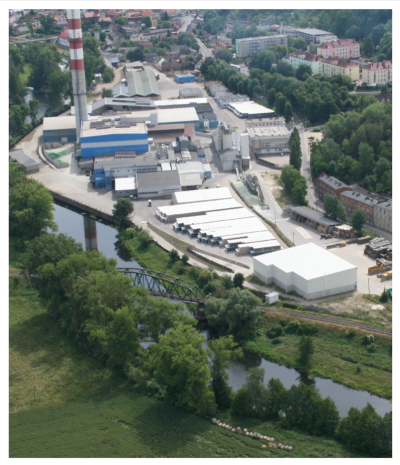
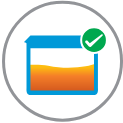
Project type:
Low-carbon melting
Project name:
Efficient Furnace AGP-Wyszkow (Furnace 1)
Project location:
Wyszkow, Poland
Project aim:
To build a highly efficient regenerative furnace and to minimise carbon emissions from the glass production process.
Key benefits:
AGP-Wyszkow's efficient regenerative furnace aims to reduce carbon emissions by c. 34%.
Description:
A conversion from recuperative to regenerative furnace technology, reducing carbon emissions by 34%.
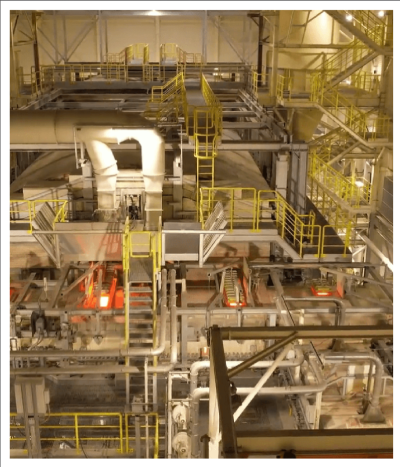
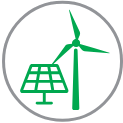
Project type:
Renewable Electricity
Project name:
PPA for wind-generated renewable electricity
Project location:
Limmared, Sweden
Project aim:
To secure a supply of 100% renewable energy for AGP's European operations.
Key benefits:
The Sweden wind-generated renewable energy project will cover c. 40% of AGP-Europe's power load.
Description:
AGP has entered a ten year renewable energy PPA with RPC's 161MW Vitberget wind project in Sweden. It will cover approximately 40% of AGP-Europe's power load and is an incremental step towards achieving AGP's goal of transitioning to 100% renewable electricity by 2030.
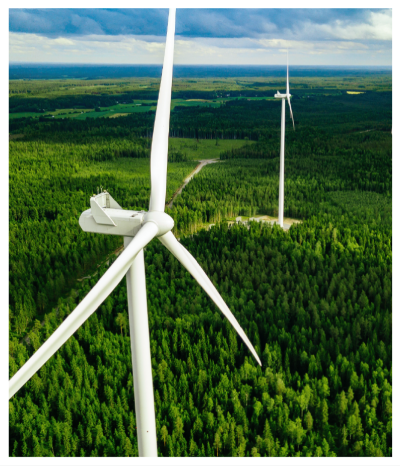
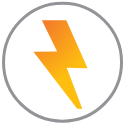
Project type:
Energy
Project name:
Hydrogen Electrolyser AGP-Limmared
Project location:
Limmared, Sweden
Project aim:
To replace 18% natural gas in the furnace with hydrogen produced using renewable electricity, reducing the carbon footprint of a large spirits customer's glass bottles by 14%.
Key benefits:
By replacing 18% natural gas in the furnace with hydrogen produced using renewable electricity, the carbon footprint of a large spirits customer's glass bottles will be reduced by 14%.
Description:
AGP has partnered with a large spirits customer to replace 18% natural gas with hydrogen produced using renewable electricity, in the furnace at the AGP-Limmared facility in Sweden. By installing a hydrogen electrolyser onsite, AGP will produce a continuous supply of hydrogen produced using renewable electricity to the furnace. It aims to reduce the overall carbon footprint of glass containers by 14%, saving approximately 4,400 tonnes of CO2 each year.
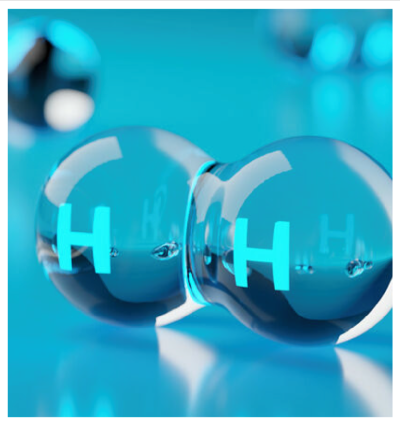
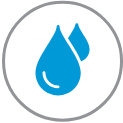
Project type:
Water
Project name:
Closed Loop Water Cooling Process
Project location:
Limmared, Sweden
Project aim:
To deliver a substantial reduction in surface water usage.
Key benefits:
The Closed Loop Water Cooling system replaces water with air to cool down the production process. This reduces water usage.
Description:
By installing a two-step, closed-loop, air and water-cooling system, air replaces water previously taken from the nearby river, to cool down the production process, delivering a 66% reduction in surface water usage compared with 2021.
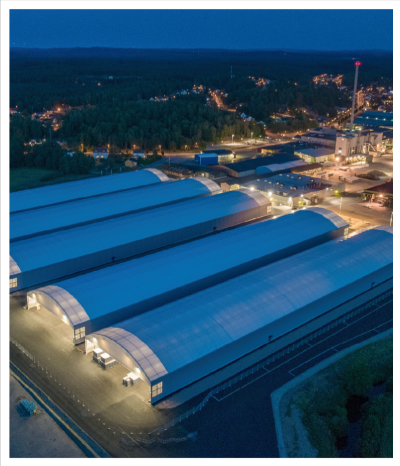
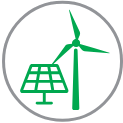
Project type:
Renewable Electricity
Project name:
VPPA Bulgaria
Project location:
Bulgaria
Project aim:
To deliver a substantial reduction in surface water usage.
Key benefits:
To secure a long-term supply of renewable electricity with a solar photovoltaic project in Bulgaria, securing renewable electricity for AGP's glass manufacturing operations across Europe from April 2026.
Description:
The VPPA - one of the first to be signed in Bulgaria - is intended to provide 110 GWh per year of renewable electricity to AGP-Europe, over 12 years. It complements AGP-Europe's renewable energy supply from wind power, secured in Sweden early in 2024. Together, thanks to their different sources, they are designed to provide AGP-Europe with a consistent renewable power supply throughout the year.
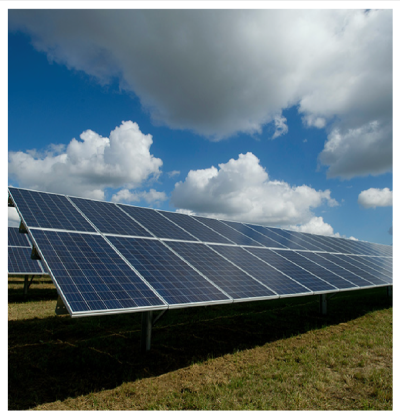
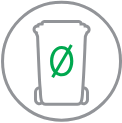
Project type:
Waste
Project name:
Zero Waste to Landfill
Project location:
Bad Münder, Germany
Project aim:
To recycle ≥95% of operational waste from each AGP facility.
Key benefits:
Eliminating operational waste from the glassmaking process will reduce AGP’s ecological impact.
Description:
Ardagh Glass Packaging’s Zero Waste to Landfill status recognises the diversion of operational waste from its facilities away from landfills, and the environment. Thirteen AGP-Europe facilities have already reached this status, with the goal for all facilities across AGP-Europe to achieve this by 2030.
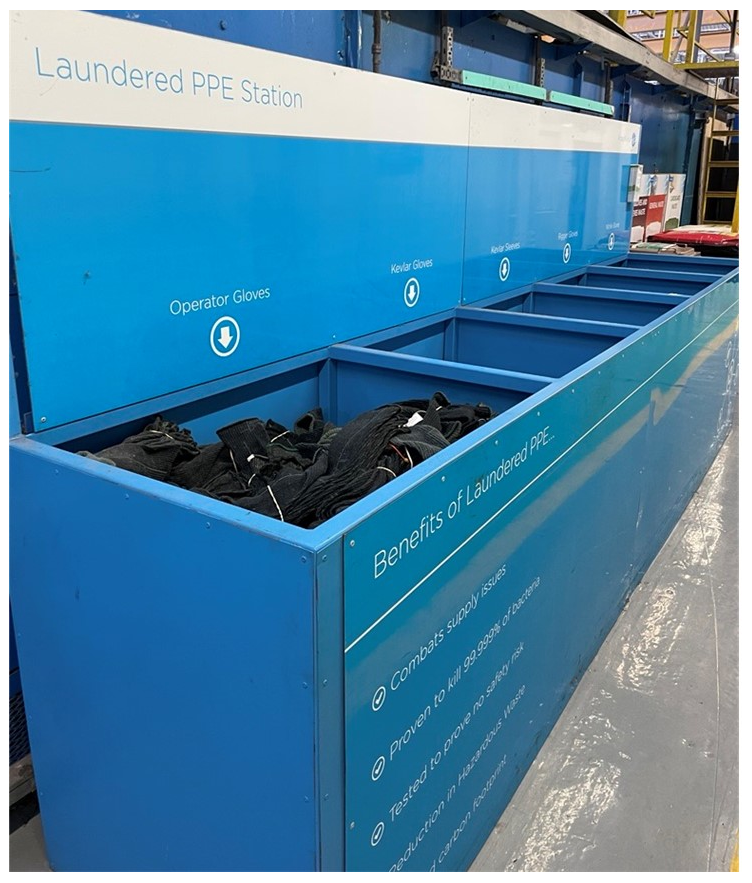
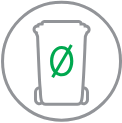
Project type:
Waste
Project name:
Zero Waste to Landfill
Project location:
Barnsley, UK
Project aim:
To recycle ≥95% of operational waste from each AGP facility.
Key benefits:
Eliminating operational waste from the glassmaking process will reduce AGP’s ecological impact.
Description:
Ardagh Glass Packaging’s Zero Waste to Landfill status recognises the diversion of operational waste from its facilities away from landfills, and the environment. Thirteen AGP-Europe facilities have already reached this status, with the goal for all facilities across AGP-Europe to achieve this by 2030.
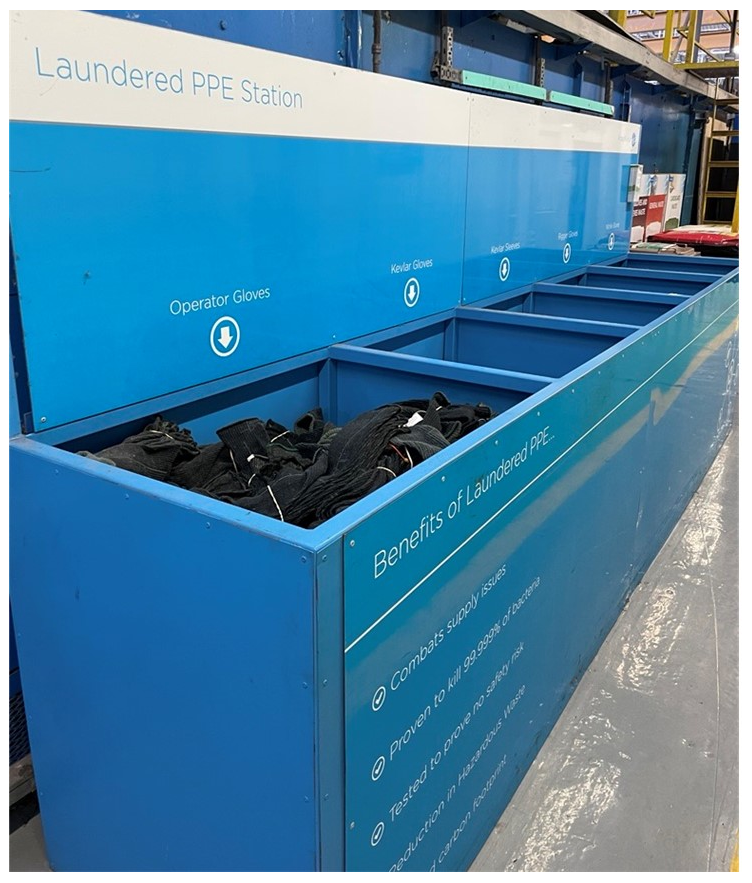
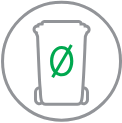
Project type:
Waste
Project name:
Zero Waste to Landfill
Project location:
Doncaster, UK
Project aim:
To recycle ≥95% of operational waste from each AGP facility.
Key benefits:
Eliminating operational waste from the glassmaking process will reduce AGP’s ecological impact.
Description:
Ardagh Glass Packaging’s Zero Waste to Landfill status recognises the diversion of operational waste from its facilities away from landfills, and the environment. Thirteen AGP-Europe facilities have already reached this status, with the goal for all facilities across AGP-Europe to achieve this by 2030.
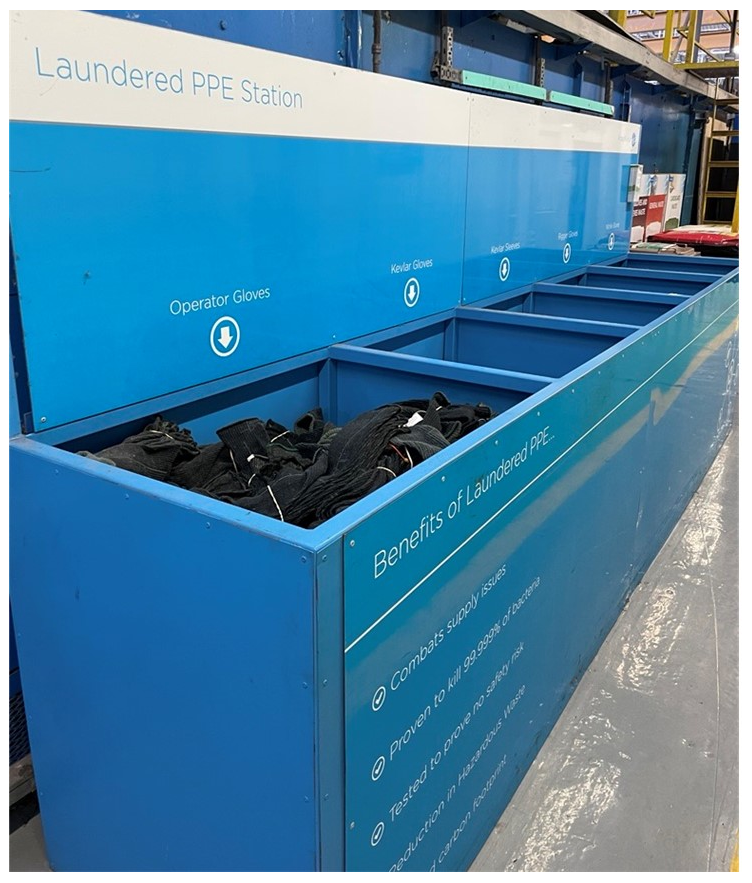
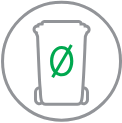
Project type:
Waste
Project name:
Zero Waste to Landfill
Project location:
Drebkau, Germany
Project aim:
To recycle ≥95% of operational waste from each AGP facility.
Key benefits:
Eliminating operational waste from the glassmaking process will reduce AGP’s ecological impact.
Description:
Ardagh Glass Packaging’s Zero Waste to Landfill status recognises the diversion of operational waste from its facilities away from landfills, and the environment. Thirteen AGP-Europe facilities have already reached this status, with the goal for all facilities across AGP-Europe to achieve this by 2030.
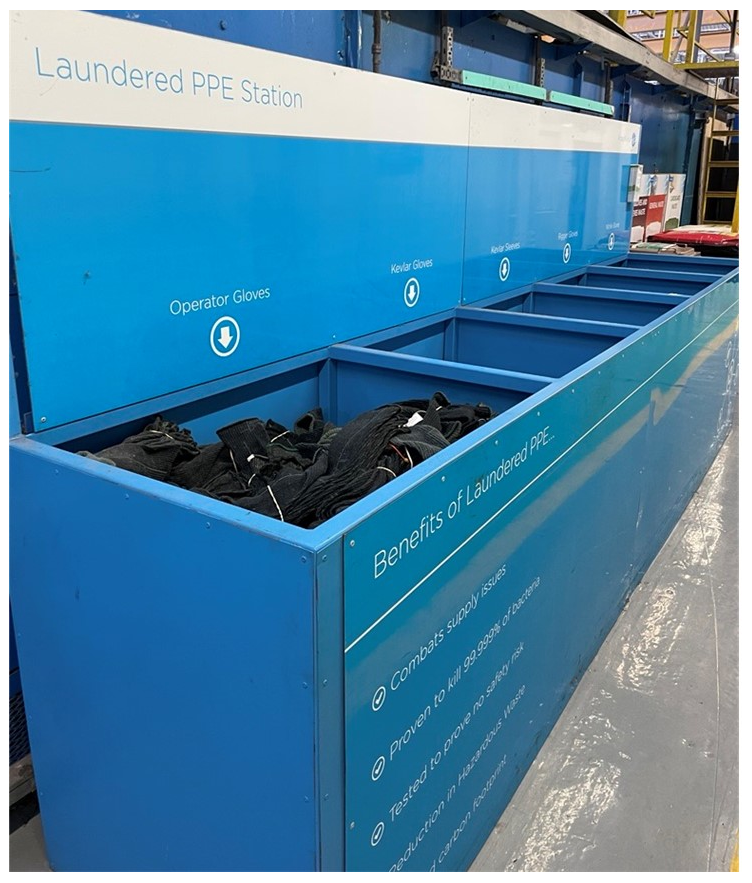
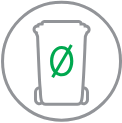
Project type:
Waste
Project name:
Zero Waste to Landfill
Project location:
Germersheim, Germany
Project aim:
To recycle ≥95% of operational waste from each AGP facility.
Key benefits:
Eliminating operational waste from the glassmaking process will reduce AGP’s ecological impact.
Description:
Ardagh Glass Packaging’s Zero Waste to Landfill status recognises the diversion of operational waste from its facilities away from landfills, and the environment. Thirteen AGP-Europe facilities have already reached this status, with the goal for all facilities across AGP-Europe to achieve this by 2030.
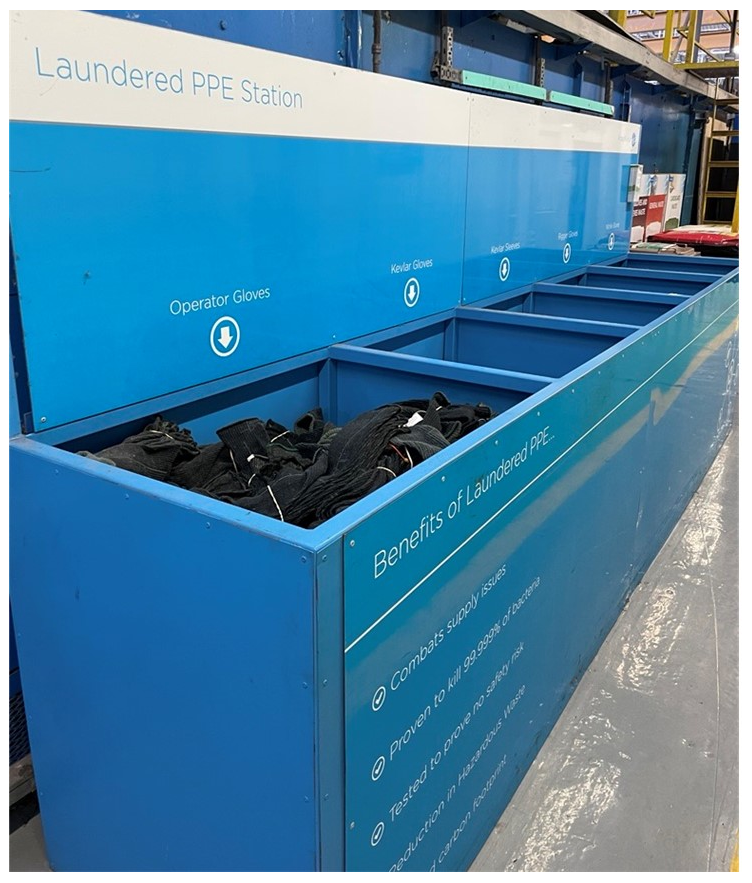
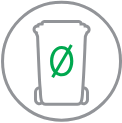
Project type:
Waste
Project name:
Zero Waste to Landfill
Project location:
Knottingley, UK
Project aim:
To recycle ≥95% of operational waste from each AGP facility.
Key benefits:
Eliminating operational waste from the glassmaking process will reduce AGP’s ecological impact.
Description:
Ardagh Glass Packaging’s Zero Waste to Landfill status recognises the diversion of operational waste from its facilities away from landfills, and the environment. Thirteen AGP-Europe facilities have already reached this status, with the goal for all facilities across AGP-Europe to achieve this by 2030.
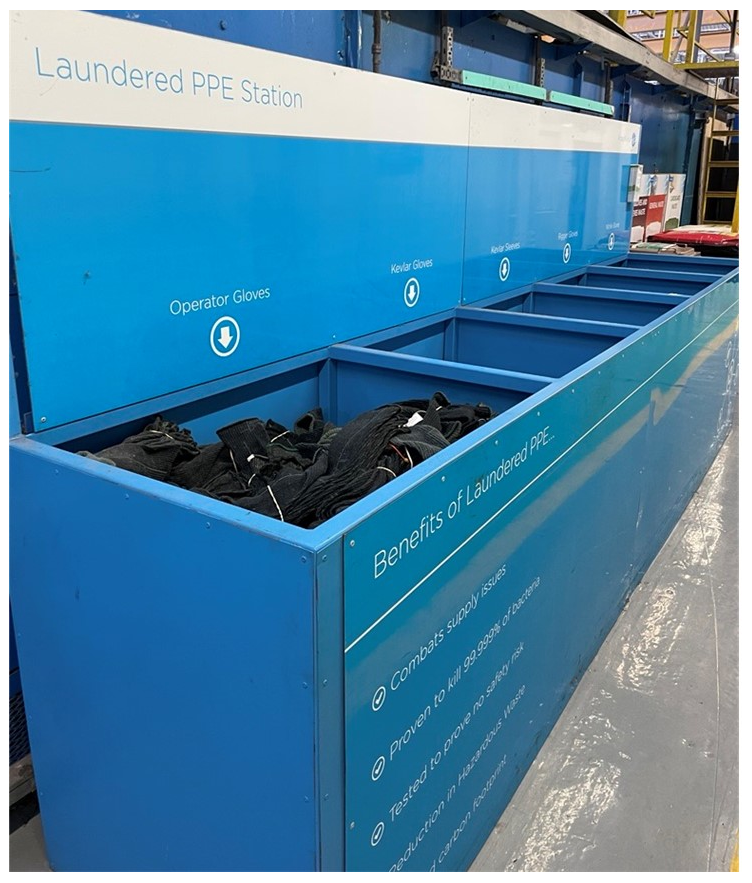
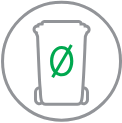
Project type:
Waste
Project name:
Zero Waste to Landfill
Project location:
Lünen, Germany
Project aim:
To recycle ≥95% of operational waste from each AGP facility.
Key benefits:
Eliminating operational waste from the glassmaking process will reduce AGP’s ecological impact.
Description:
Ardagh Glass Packaging’s Zero Waste to Landfill status recognises the diversion of operational waste from its facilities away from landfills, and the environment. Thirteen AGP-Europe facilities have already reached this status, with the goal for all facilities across AGP-Europe to achieve this by 2030.
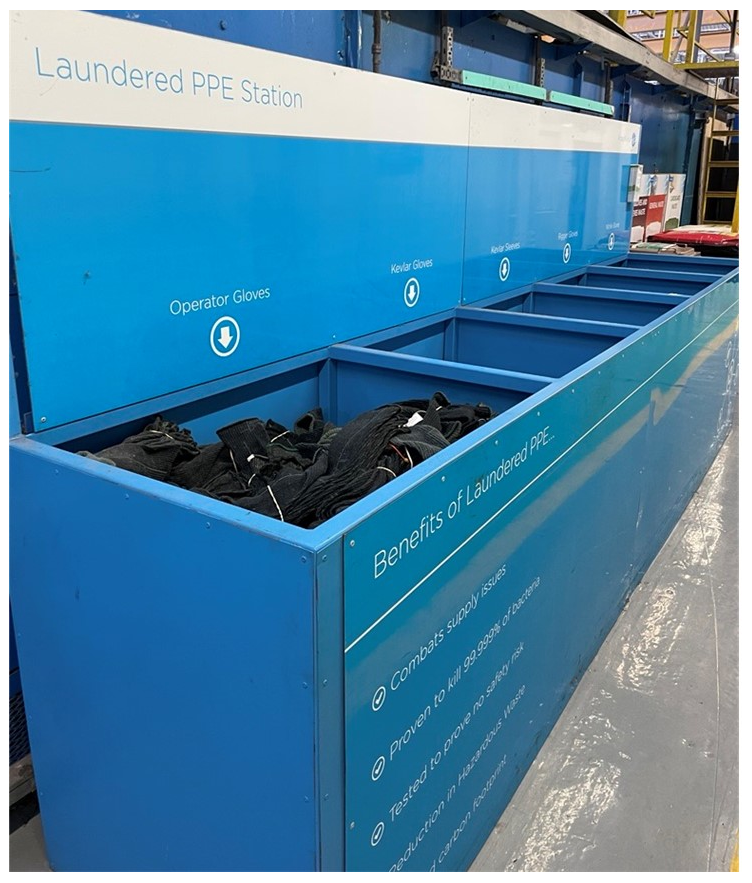
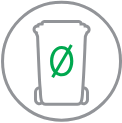
Project type:
Waste
Project name:
Zero Waste to Landfill
Project location:
Montorio al Vomano (IT-MAV)
Project aim:
To recycle ≥95% of operational waste from each AGP facility.
Key benefits:
Eliminating operational waste from the glassmaking process will reduce AGP’s ecological impact.
Description:
Ardagh Glass Packaging’s Zero Waste to Landfill status recognises the diversion of operational waste from its facilities away from landfills, and the environment. Thirteen AGP-Europe facilities have already reached this status, with the goal for all facilities across AGP-Europe to achieve this by 2030.
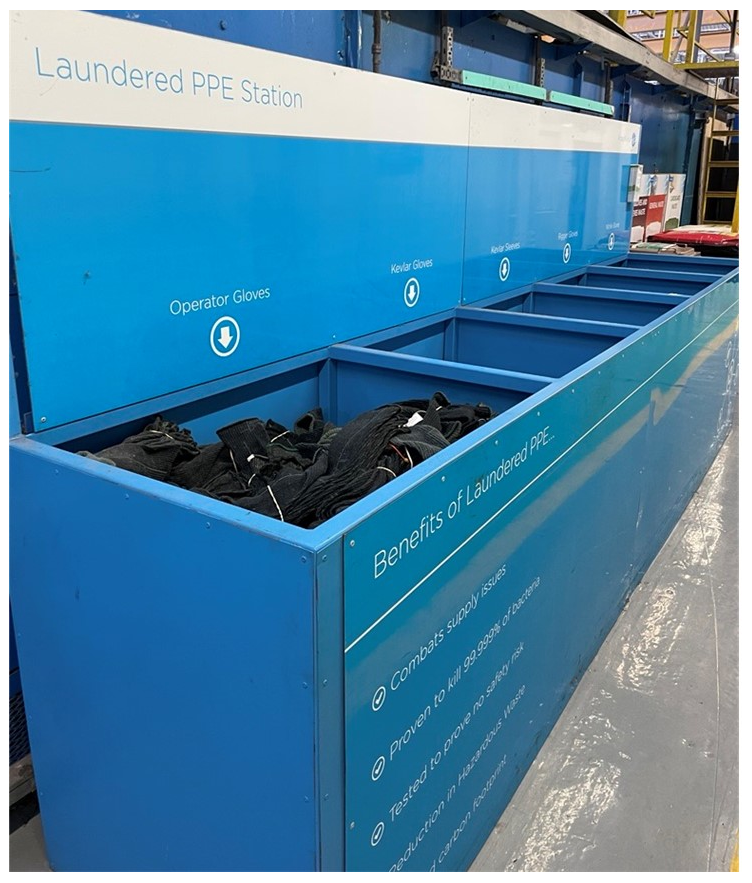
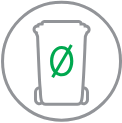
Project type:
Waste
Project name:
Zero Waste to Landfill
Project location:
Neuenhagen, Germany
Project aim:
To recycle ≥95% of operational waste from each AGP facility.
Key benefits:
Eliminating operational waste from the glassmaking process will reduce AGP’s ecological impact.
Description:
Ardagh Glass Packaging’s Zero Waste to Landfill status recognises the diversion of operational waste from its facilities away from landfills, and the environment. Thirteen AGP-Europe facilities have already reached this status, with the goal for all facilities across AGP-Europe to achieve this by 2030.
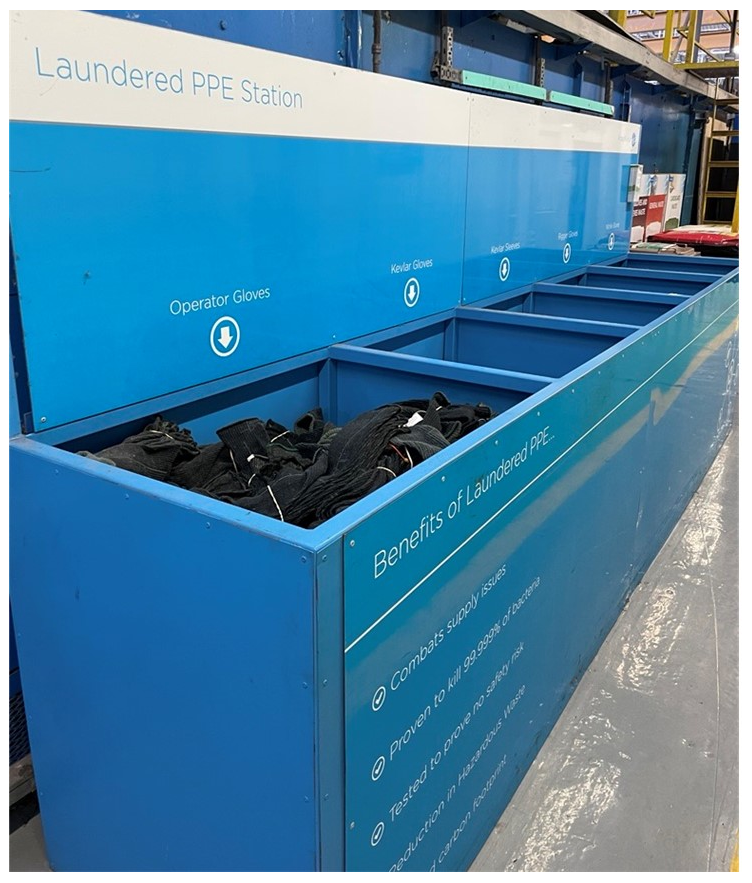
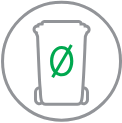
Project type:
Waste
Project name:
Zero Waste to Landfill
Project location:
Nienburg, Germany
Project aim:
To recycle ≥95% of operational waste from each AGP facility.
Key benefits:
Eliminating operational waste from the glassmaking process will reduce AGP’s ecological impact.
Description:
Ardagh Glass Packaging’s Zero Waste to Landfill status recognises the diversion of operational waste from its facilities away from landfills, and the environment. Thirteen AGP-Europe facilities have already reached this status, with the goal for all facilities across AGP-Europe to achieve this by 2030.
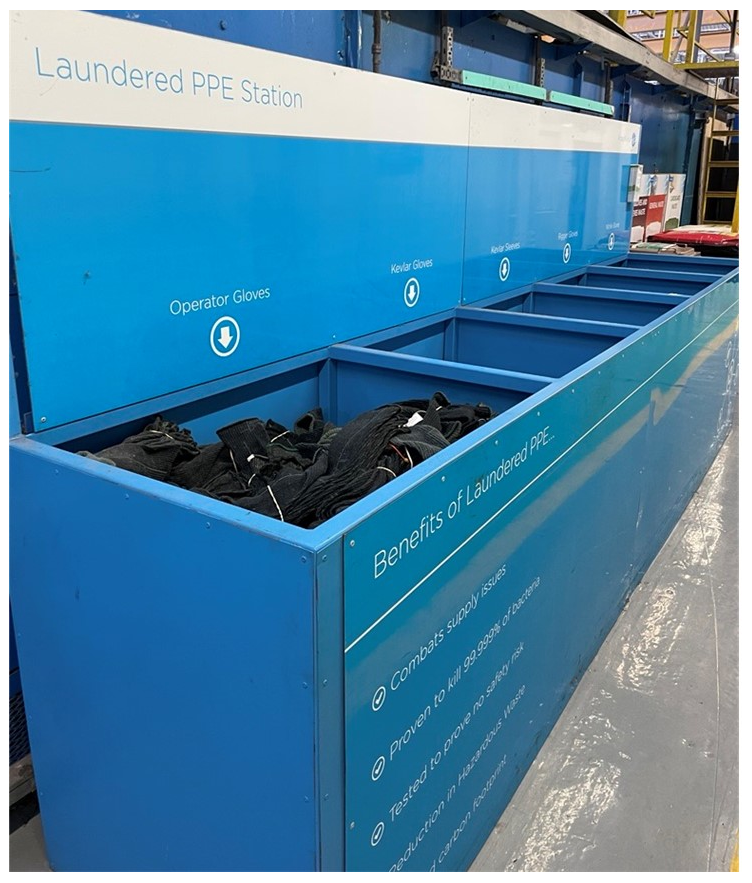
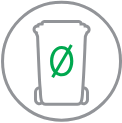
Project type:
Waste
Project name:
Zero Waste to Landfill
Project location:
Obernkirchen, Germany
Project aim:
To recycle ≥95% of operational waste from each AGP facility.
Key benefits:
Eliminating operational waste from the glassmaking process will reduce AGP’s ecological impact.
Description:
Ardagh Glass Packaging’s Zero Waste to Landfill status recognises the diversion of operational waste from its facilities away from landfills, and the environment. Thirteen AGP-Europe facilities have already reached this status, with the goal for all facilities across AGP-Europe to achieve this by 2030.
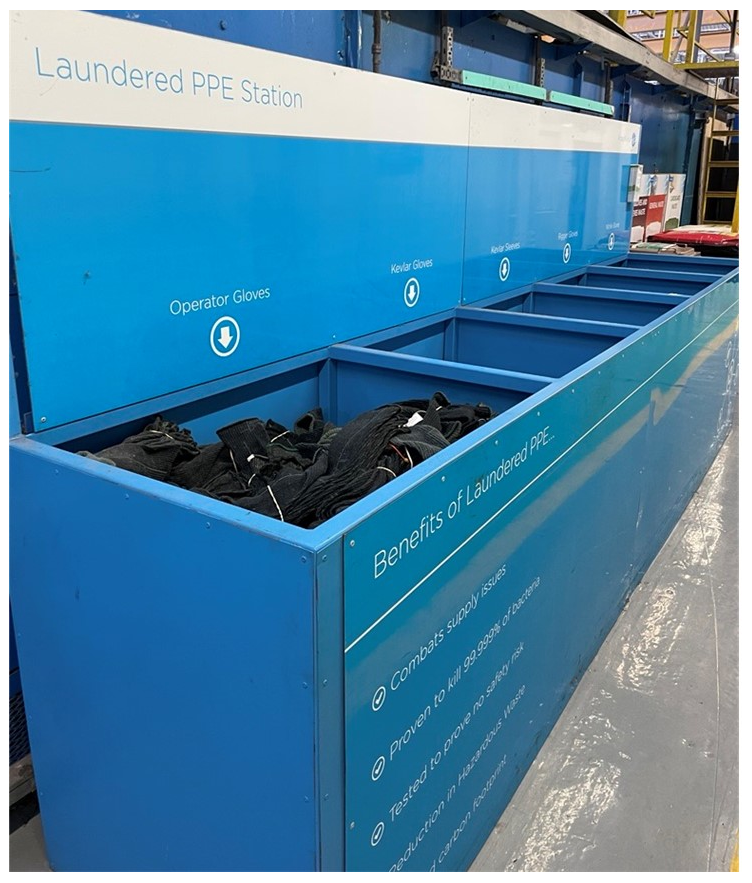
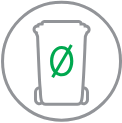
Project type:
Waste
Project name:
Zero Waste to Landfill
Project location:
Wahlstedt, Germany
Project aim:
To recycle ≥95% of operational waste from each AGP facility.
Key benefits:
Eliminating operational waste from the glassmaking process will reduce AGP’s ecological impact.
Description:
Ardagh Glass Packaging’s Zero Waste to Landfill status recognises the diversion of operational waste from its facilities away from landfills, and the environment. Thirteen AGP-Europe facilities have already reached this status, with the goal for all facilities across AGP-Europe to achieve this by 2030.
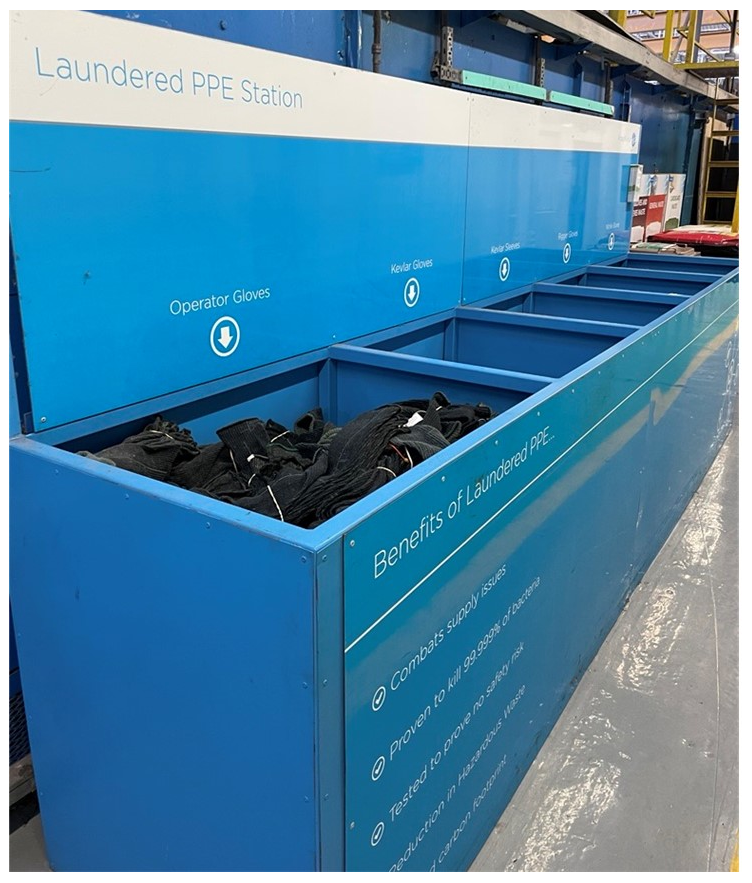